Thermoforming, vacuum forming, pressure forming, CNC part machining — these manufacturing methods have made up the SSI toolkit since the 1970s. We use the latest state-of-the-art forming machinery and techniques along with our expert assembly process to create complex parts at a high level of detail.
See why top OEMs and high-tech specialty device manufacturers choose SSI thermoforming services for critical components:
Book a meeting to talk details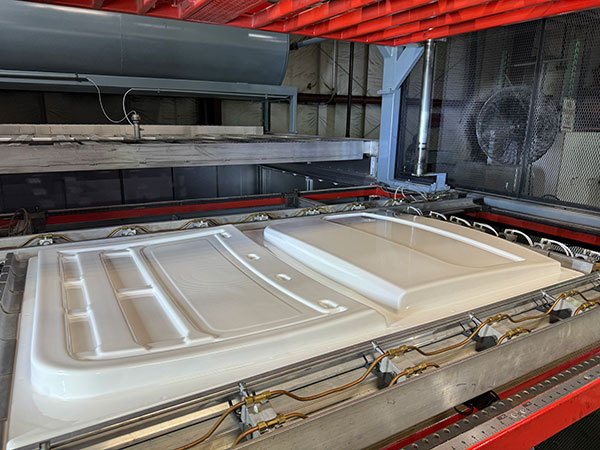
Thermoforming and Vacuum Forming
Thermoforming and vacuum forming are often used synonymously, but it’s more accurate to say that thermoforming describes the general process of molding heated plastic materials, while vacuum forming specifies a process in which those materials are pressurized or vacuumed over a mold and cooled to retain their new shape.
While thermoforming and vacuum forming are not typically the best methods for mass production or manufacturing hollow parts, they are great choices for a variety of applications and rank highly among other plastic molding methods on affordability, speed, range across small and large parts, level of detail, and number of material options.
Why Choose Thermoforming?

Quick
Thermoforming is a fast alternative to many other plastic molding methods, such as rotomolding and compression molding. Custom part production takes a matter of days, rather than the months you might wait if using another method.

Economical
Plastic is more cost-effective than fiberglass or metal, and vacuum forming molds are relatively inexpensive, making thermoforming a much smaller investment than other forming methods.

Versatile
Thermoforming can produce varied components in all sizes, from simple trays to highly detailed flight-critical components.

Durable
Plastics used in thermoforming can stand up to environmental pressures and resist degradation without regular maintenance.
Material Options for Thermoforming
- ABS (Acrylonitrile Butadiene Styrene)
- Acrylic (Polymethyl Methacrylate)
- PETG (Polyethylene Terephthalate Glycol)
- PP (Polypropylene)
- PVC (Polyvinyl Chloride)
- TPO (Thermoplastic Polyolefin)
- KYDEX™ (PMMA / PVC blend)
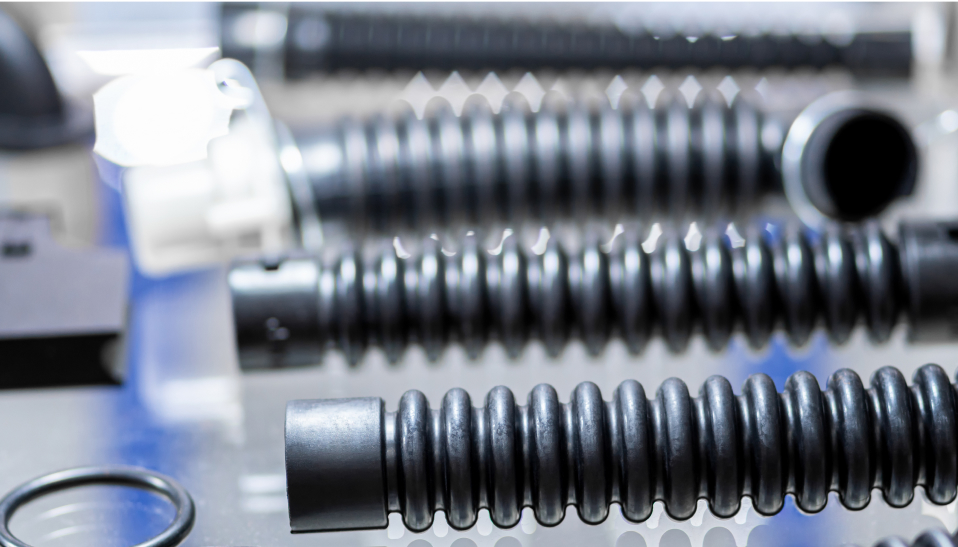
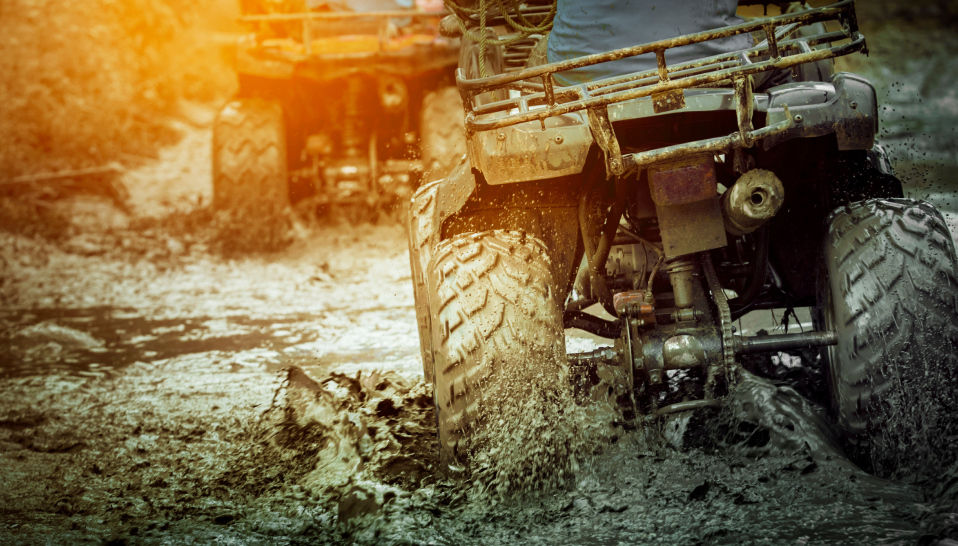
Thermoforming Applications
Need a plastic part? We can thermoform it for you. The processes we use can be applied to just about any component in any industry. Here are a few we work with regularly:
Recreation
ATV and RV components
Fishing rod and tackle storage
Bodywork for scooters
Golf cart parts
Coolers
Marine
Transom trims
Piling and post caps
Coaming boxes
Rod boxes
Storage cabinets
Dash panels
Electrical Enclosures
Window Trims
Industrial
Belt and machine guards
Access doors and panels
Electrical connection enclosures
Industrial piling and pole covers
Interior and exterior machinery parts
Medical
Face shields
Medical trays
Cadaver bins
Instrument housings
Medical Carts
Therapeutic devices
Dunnage and containers
Catch bins and waste receptacles
Organizers and tools trays
Environment covers
Stacking or nesting parts
Storage bins and tubs
Home and garden
Growing pots
Seeding trays
Garden ornaments
Concrete forms
Landscaping and gardening tools
Get more information on the markets we serve: see our industries.
Available Specifications
Sizes
- Width: Up to 5 ft
- Length: Up to 9 ft
- Thickness: From 1/16” to over ½”
Strength
Our plastic components often match or exceed the strength of their fiberglass or metal counterparts — plus, plastics are more durable and don’t require maintenance.
Aesthetics
Our formed plastic parts can be produced in your desired color — no need for prepping, coating, or painting.
Secondary Services
We offer full assembly of multi-component parts and can package ready-to-use units. We can also pre-install hardware, including:
- Mounting studs
- Threaded inserts
- Hinges
- Latches
- Locks
- Props
- Mounts
- Grommets
- And more — just ask!