Thermoforming vs. Injection Molding:
Cost, Lead Times & More
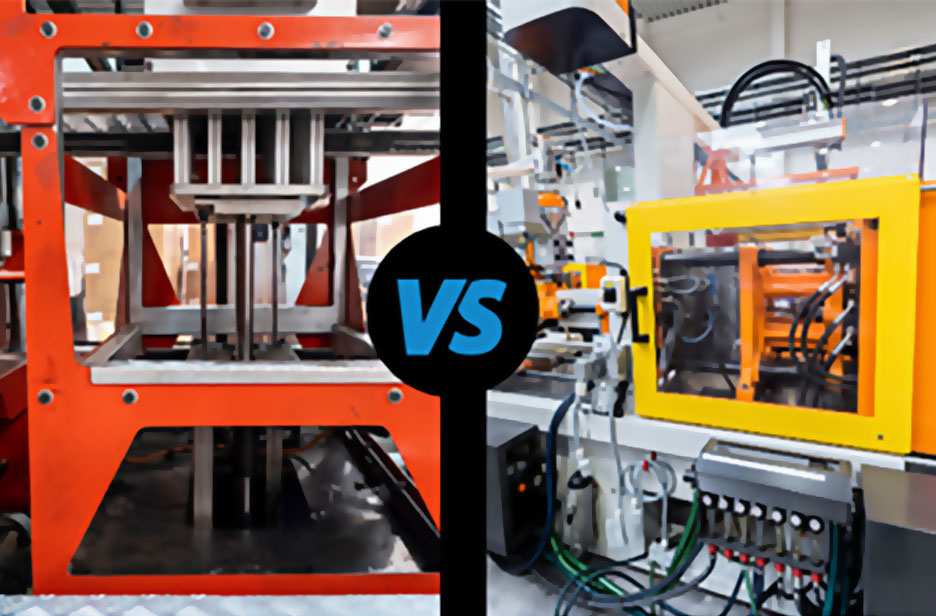
Trying to determine the right way forward with your plastic manufacturing project? Explore injection molding versus thermoforming — particularly vacuum forming — and learn:
Processes: Distinguishing Thermoforming and Injection Molding
While thermoforming can be a general umbrella term for plastic forming processes that involve heat — and injection molding does technically involve a heating process — we don’t place injection molding under the thermoforming umbrella. Instead, we consider thermoforming and injection molding to be two distinct methods of plastic forming, primarily due to fundamental differences at the process level.
Thermoforming Process
“In general, ‘thermoforming’ implies that the molding process is performed on an existing shape,” says John Donato, SSI President. “In SSI’s case, this shape is a sheet of plastic, though other shapes can be thermoformed, too. Forming a flared end on a piece of plastic tubing using heat would be considered thermoforming, for example.”
For example, in this video of custom seat base vacuum forming for an SSI client, you can see a black sheet of plastic being lowered and “vacuumed” onto the mold:
Injection Molding Process
Injection molding does not reshape plastic; it creates plastic parts with molten material using a specialized injection molding machine (IMM).
Injection molded pieces start the forming process as plastic pellets. These are fed into the IMM and melted within a heated barrel until they become molten. An auger, or injection screw, pushes the molten plastic and injects it at high pressure into a specially designed mold, where the plastic will then cool and solidify in the desired shape.
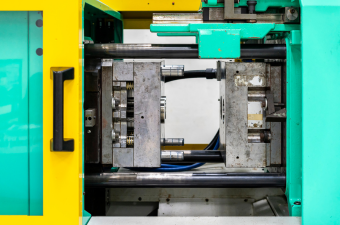
Materials: Plastics Suited to Thermoforming vs. Injection Molding
“Plastic material choices for both thermoforming and injection molding are specific to the process used. Those differences need to be considered when designing the part,” says Donato.
Thermoforming Materials
- Materials begin as plastic sheets.
- Not all plastics can be used, but a wide range is suitable for thermoforming.
- Sheets allow special surfaces to be applied automatically in the process of thermoforming. These can include haircell finish, embossed patterns, and even special laminated treatments such as woodgrain, brushed metal, high gloss, etc.
- Forming from a sheet under vacuum imparts very little stress on the material, making the end product very stable and durable.
- Changing the material used is simple, as tooling process adjustments are easy (and sometimes not necessary).
Injection Molding Materials
- Materials begin as plastic pellets.
- Plastics used must be capable of melting and flowing into mold cavities.
- In general, the plastic type, color, and texture are limited. While some intricate injection molding processes can mold variations in color and material, these are usually expensive and complex.
- Forcing molten plastic into the mold cavities imparts considerable stress on the parts. In many cases, this is not a problem, but it can make parts dimensionally unstable.
- Material changes often require injection mold rework or, worse — a new mold.
Advantages of Injection Molding
Less “Waste”
Thermoformed parts are formed and then cut out, creating much more waste material than you see in injection molding.
“It should be noted, however,” says Donato, “That this ‘waste’ is easily ground up and reused to make new products. It goes to good use. so it’s not really wasted.”
Shorter Cycle Times
While getting started with thermoforming is faster, the actual cycle time of the injection molding process can produce more parts per hour, making it well-suited to large-quantity projects.
Supports More Complex Shapes
Some parts require extreme negative angles and complex details that thermoforming cannot achieve. Thanks to the precision chromed finish and intricate surface details of injection molds, along with the incredible pressure involved in the process, injection molding can achieve a very high level of precision and detail. Parts can be molded with inserts, hardware, and other items right in the mold.
“While this level of detail is a definite advantage in favor of injection molding,” says Donato, “It’s important to note that each level of complexity and detail comes with an associated price tag, which means there are many situations where thermoforming will be a far better choice than injection molding — especially with newer technology that allows thermoforming to create increasingly complex shapes.”
High Production Rate
Although several parts can be thermoformed at a time, injection molds often have many cavities that allow a large number of parts to be molded at the same time.
Lower Cost Per Part at High Volumes
For very high-volume runs, injection molding has a lower cost of production per part. Even though the mold cost and development is initially much higher, the higher production rate reduces the eventual part cost. Injection molding is the better choice if you can offset the initial costs with savings per part on large-quantity orders.
Advantages of Thermoforming
Lower tooling costs
Thermoforming tooling is a fraction of the price needed to create an injection mold.
Faster Timeline
Thermoforming mold development and production take days to weeks, while the injection mold process takes multiple months to design and build. You’ll generally need to make modifications after design and building are complete, pushing your end date out even further. Additionally, injection molds are increasingly produced offshore, while thermoforming molds are easily and quickly made in-house.
Better for Large Parts
Large parts are easily thermoformed but not easily injection molded. Since injection molding requires that the mold be held shut as plastic is injected, the larger the part, the greater the amount of force (measured in tons!) needed to complete the process, requiring increasingly larger IMMs.
More Flexible
Implementing changes to thermoforming molds and tools is simple, whereas making a change to your injection mold often requires a new mold to be made from scratch.
Easier Process
Setup for production is very simple and repeatable for thermoforming, while injection molding is complex and involved. This makes thermoforming the clear choice for smaller production runs.
Advanced Technology
While injection molding used to be the better choice in many more applications, thermoforming advancements have significantly closed that gap and made thermoforming a competitive alternative in many cases. These advancements include:
- Servo movement and computer controls
- Advanced heating processes using quartz technology
- Specialized mold-making materials
- Specially formulated plastic materials
Comparing Costs of Thermoforming vs. Injection Molding
Since the relationship between price per part and order size has such a large impact on the potential cost savings of thermoforming vs. injection molding, let’s look at a few examples that illustrate how the cost-effectiveness of each method can change depending on the situation.
Example 1
Imagine you need a plastic belt guard for a generator. This constitutes about 200 parts per year with a three-year product lifecycle.
For thermoforming:
- Upfront tooling investment = $2200
- Production price per part = $46.80
- Three-year cost per part = $50.46
- Three-year total spend = $30,280
For injection molding:
- Upfront tooling investment = $28,000
- Production price per part = $29.88
- Three-year cost per part = $76.54
- Three-year total spend = $45,928
In this case, thermoforming is the clear winner.
Example 2
Say you need to manufacture plastic serving spoons at about 30,000 parts per year with a three-year product lifespan.
For thermoforming:
- Upfront tooling investment = $2500
- Production price per part = $2.80
- Three-year cost per part = $2.83
- Three-year total spend = $254,000
For injection molding:
- Upfront tooling investment = $52,000
- Production price per part = $0.28
- Three-year cost per part = $0.86
- Three-year total spend = $77,200
In this case, injection molding is the clear winner.
So, Which Is More Affordable?
As you can see, it’s necessary to look at the numbers and consider every factor in your specific situation to decide whether thermoforming or injection molding will be more cost effective.
As discussed earlier, thermoforming is generally the better choice for large parts. For small parts, the answer is a bit more complicated.
“Generally,” says Donato, “Small, highly detailed parts with very high annual usage (usually in the thousands of parts per year) are a better fit for injection molding due to the low scrap rate and high throughput. However, small parts that do not have a very high usage rate can be a better fit for thermoforming since, although the production rate is less, the initial investment in tooling is much less, as are the development time and complexity of the mold.”
Making the Choice between Injection Molding and Thermoforming
In some cases, the answer is clear:
- Do you have very large parts to produce or very low quantities? Thermoforming is likely a better choice.
- Do you need to produce small, highly detailed pieces in large quantities? Injection molding is probably your best bet.
However, your situation might not be so cut and dry. You may need to weigh the advantages of thermoforming vs. injection molding for multiple factors related to your product. We recommend requesting quotes from your plastics partners so you can look at cost comparisons and see how your requirements impact your totals.
Sometimes, the right choice is both! There are many situations where thermoforming and injection molding can work together to produce the best scenario for your business. For example:
- Begin production with thermoforming, then move to injection molding when your parts need to be mass produced.
- Before diving into injection molding, thermoform your prototypes to take advantage of the shorter lead times and lower costs. If your prototype is a success and fits your needs, you may be able to move on to injection molding.
Although SSI does not injection mold, we work with an injection molding partner who can form parts for us when necessary — and in turn, we thermoform certain parts for them! If you’re unsure of the right choice for your current project, drop us a line and we’ll support you on the best path forward.