What Products Use Thermoforming? 15 Vacuum-Formed Examples
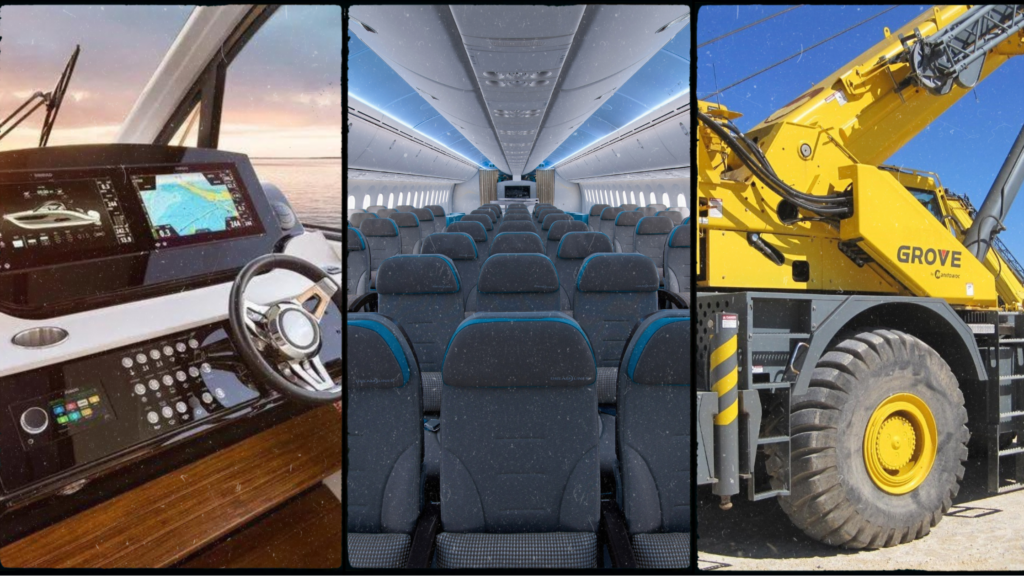
While thermoforming and vacuum forming are well-known processes for producing high-quality plastic parts, we find that many manufacturers aren’t aware of just how versatile this method is.
To showcase the diverse range of components that can be plastic-formed with vacuum pressure, we’ve rounded up 15 thermoforming product examples — some of which might surprise you!
- Body Panels: Hoods, Roof Assemblies, Guards & Doors
- Dash Panels and Instrument Pods
- Skylights and Vents
- Drain Pans
- Belt and Chain Guards
- Part Trays
- Inflow Preventers (Manhole Inserts)
- Air Ducts, Flanges, and Adaptors
- Funeral Care Trays
- Medical Items
- Mass Transit Panels
- Piling Caps (Post Caps)
- Kitchen Appliance Components
- Furniture
- RC Toys, UAVs, and Drones
1. Body Panels: Hoods, Roof Assemblies, Guards & Doors
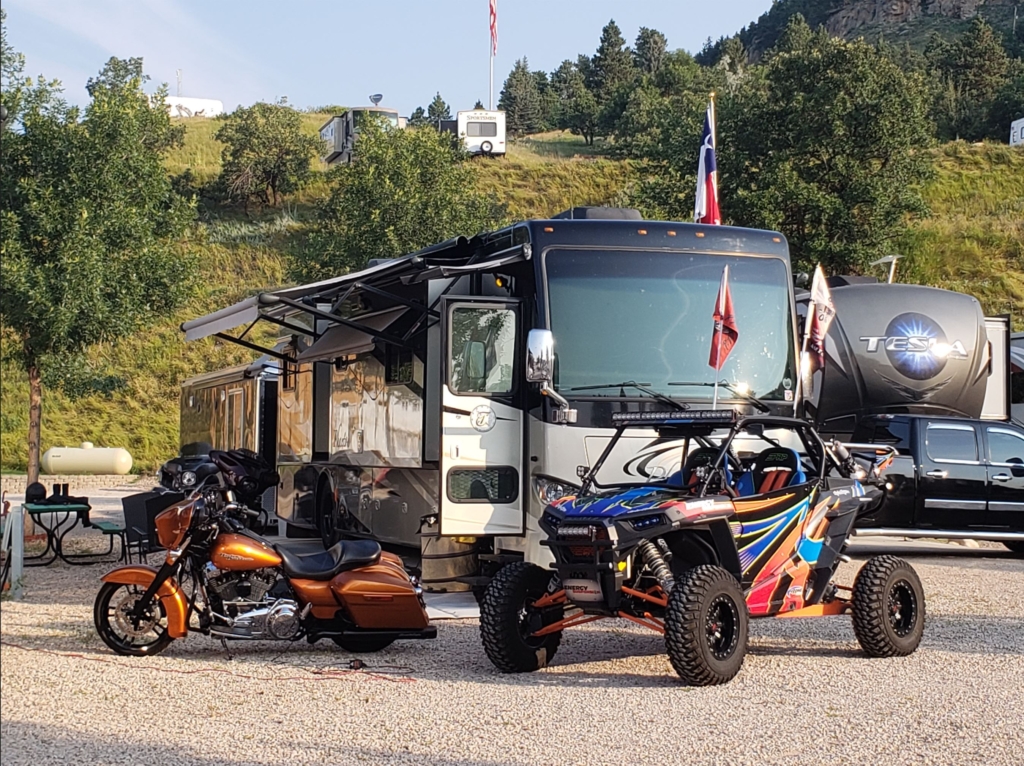
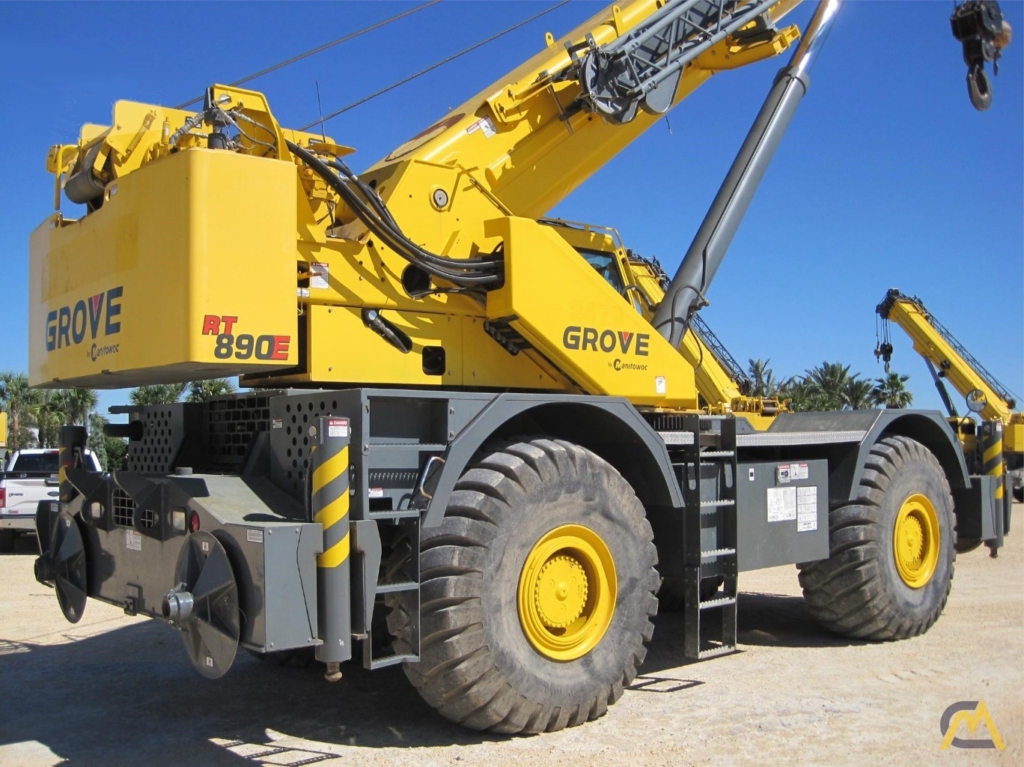
Body panels, hoods, covers, and doors for machinery may look like they’re made of metal or fiberglass — as they often were in the past — but these days, they’re usually thermoformed plastic. You can find body panels like this on machinery, including:
- Construction equipment and vehicles
- Farm equipment
- Landscaping machinery
- Material handling machine
- Floor sweepers
We’ve analyzed the benefits of plastic vs. fiberglass before in general practice, but for body panels especially, fiberglass (and metal) have fallen out of favor because thermoplastics offer significant advantages, including a lower price point for production, reduced weight, and better sustainability.
One of the most enticing benefits for machinery manufacturers is that thermoformed body panels don’t require the effort that fiberglass and metal do to retain a superior surface finish. Vacuum-formed parts have their color and finish (gloss or texture) “molded in” during production. In other words, these elements are part of the plastic itself, sparing manufacturers the need to paint parts. This benefit also gets passed on to the end user; thermoplastic body panels are highly resistant to impact and scratch damage that would normally require dent repair or paint touch-ups.
2. Dash Panels and Instrument Pods
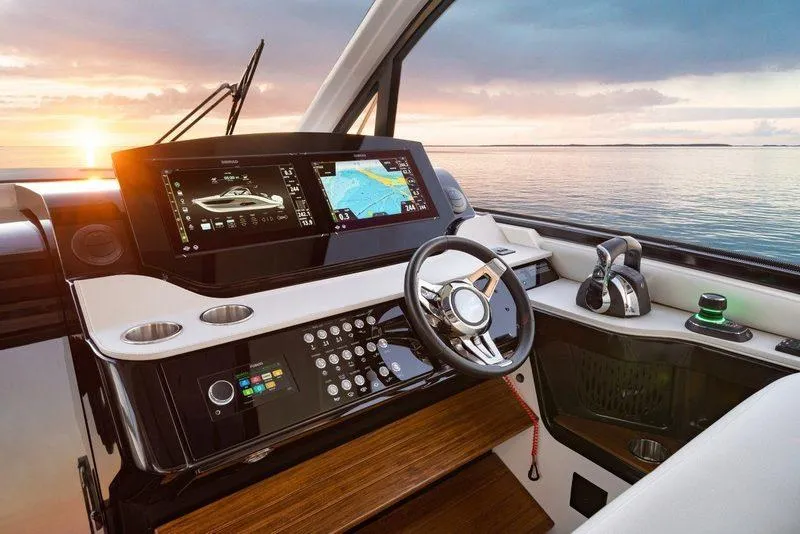
Attractive and tough, thermoformed gauge pads and instrument panels are commonplace in automotive, marine, ATV, and equipment applications. While small, high-use parts are typically injection molded, larger components are usually thermoformed for a few reasons:
- Large parts are generally better suited to thermoforming vs. injection molding.
- These parts often have a textured or “haircell” finish; as we saw with body panels, thermoforming makes it extremely easy to achieve this effect.
- It’s easy to match all of the components of the dash or control console match since they are formed from the same material.
- Extra features like threshed inserts and recesses for cutouts can be added during the production process.
- Thermoformed dash panels lend themselves well to being upholstered or painted.
3. Skylights and Vents
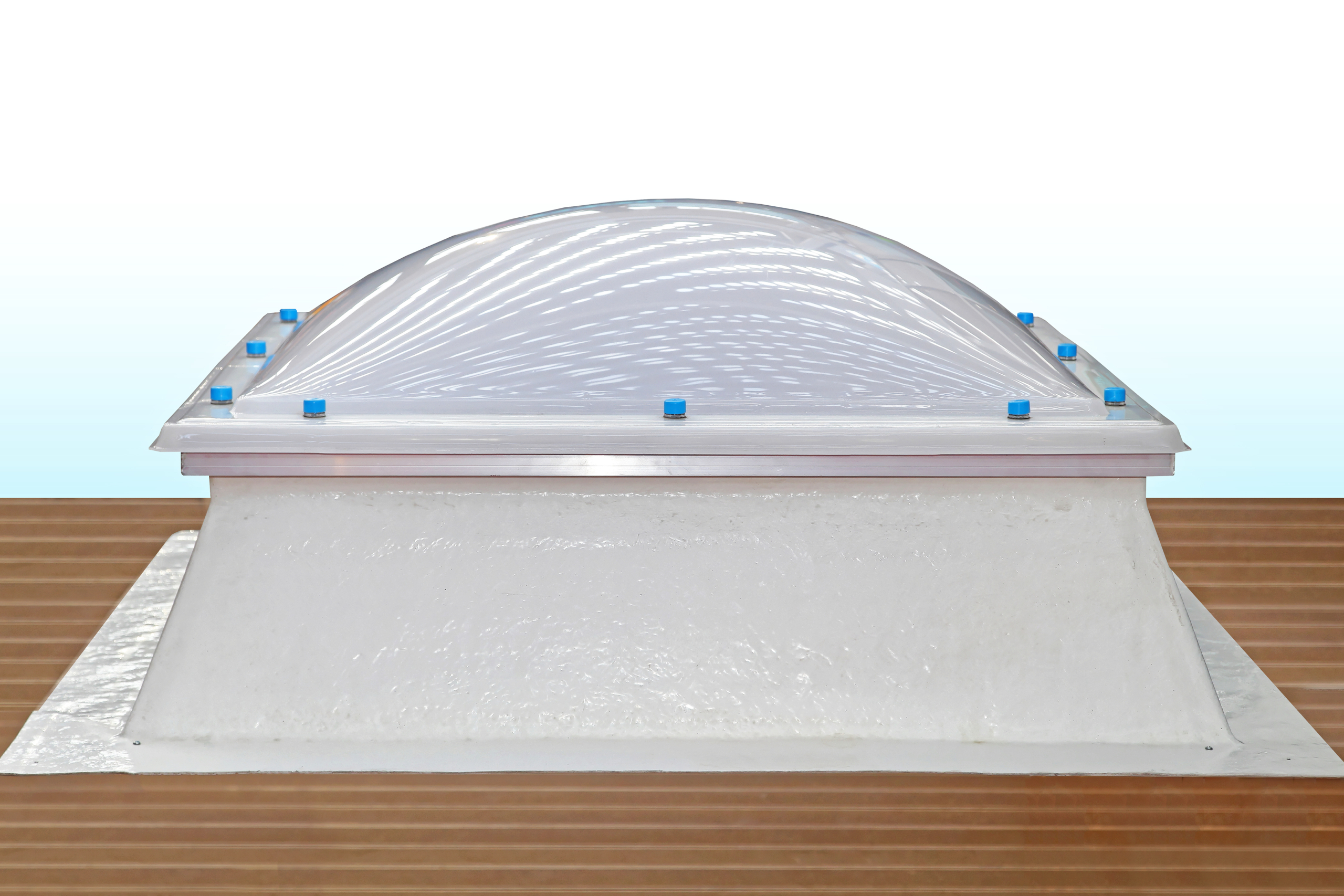
Clear and strong, polycarbonate is a great material for skylights and vents when glass isn’t an option. Polycarbonate is highly thermoformable, and for these particular products, thermoforming is a good fit because it introduces little-to-no stress during forming, which improves the lifespan of the window and does not require contact with a mold surface during production, leaving the part clear and smooth.
4. Drain Pans
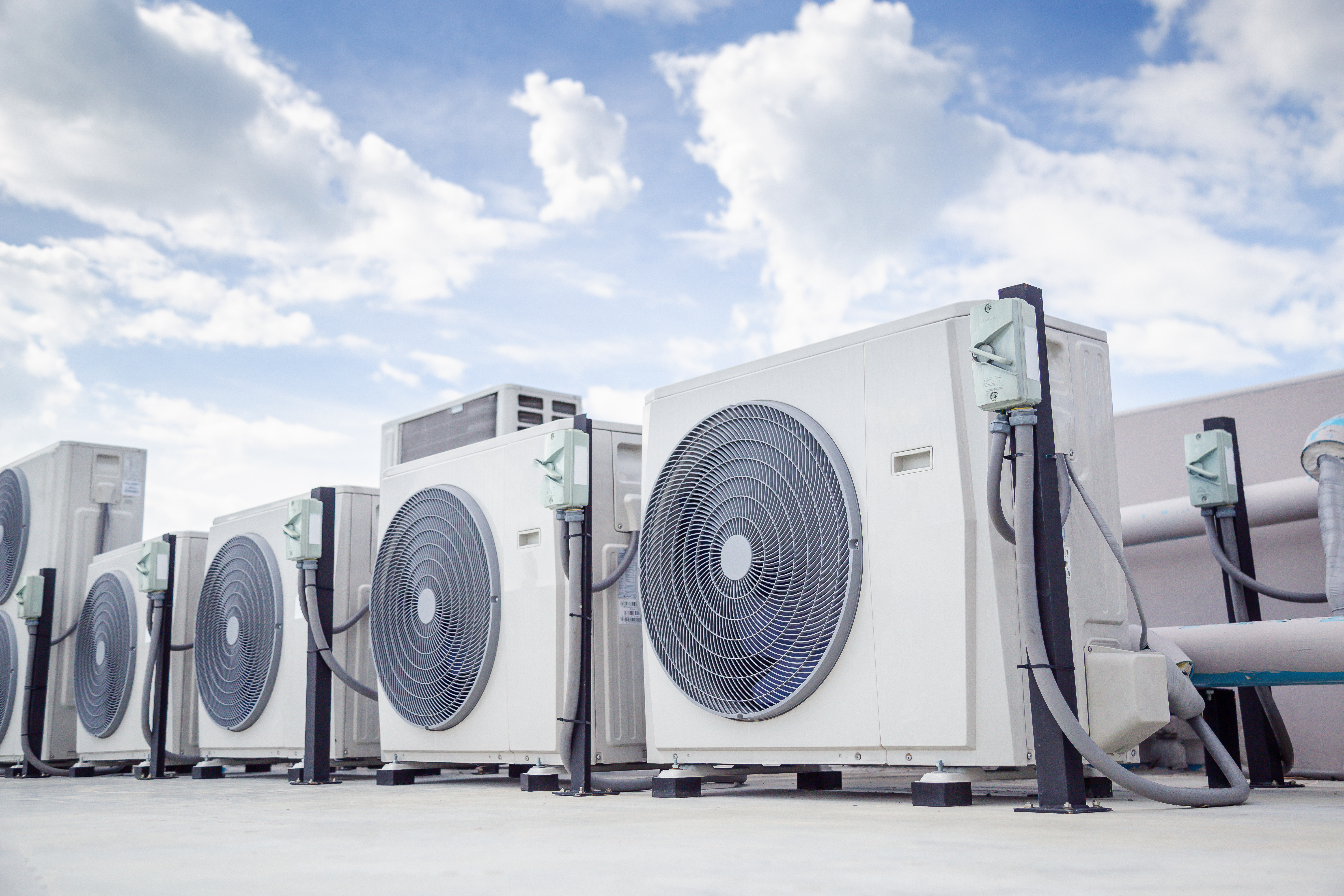
Drain pans for appliances, HVAC equipment, pet cages, pump systems, and other catch pans are often thermoformed because of their size. The relatively low cost of thermoforming tooling lends itself well to large parts (whereas an injection mold for large pans would be cost-prohibitive). Thermoformed catch pans are tough, flexible, recyclable, chemical resistant, and can have drain wells or other features molded in.
5. Belt and Chain Guards
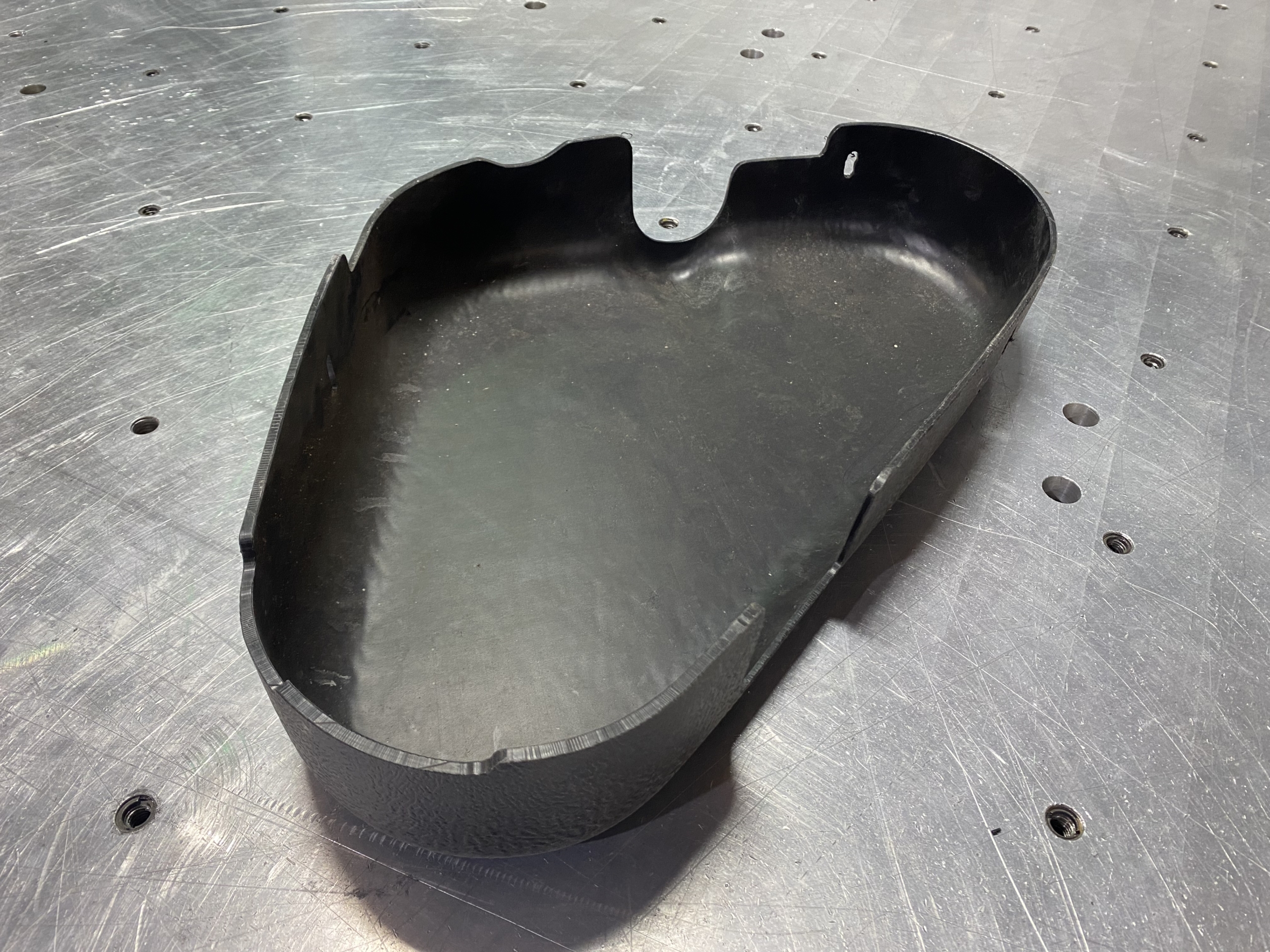
Belt and chain guards on a variety of products — from generator belts and ATV guards to exercise equipment and bicycles — benefit from thermoforming because of the following advantages:
- Tooling costs for these items are very low
- It’s easy to add additional features to the mold
- Thermoplastics used for guards are weatherable, tough, and attractive
- Guards can be easily machined to accept mounting hardware
- The materials used offer high levels of injury protection for a low cost
6. Part Trays
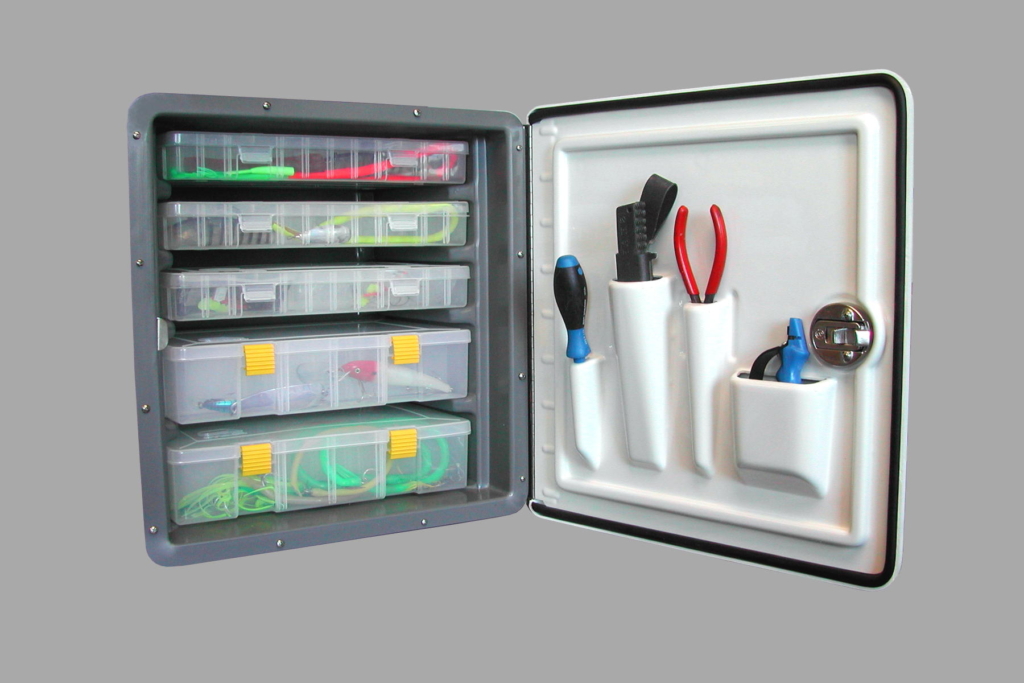
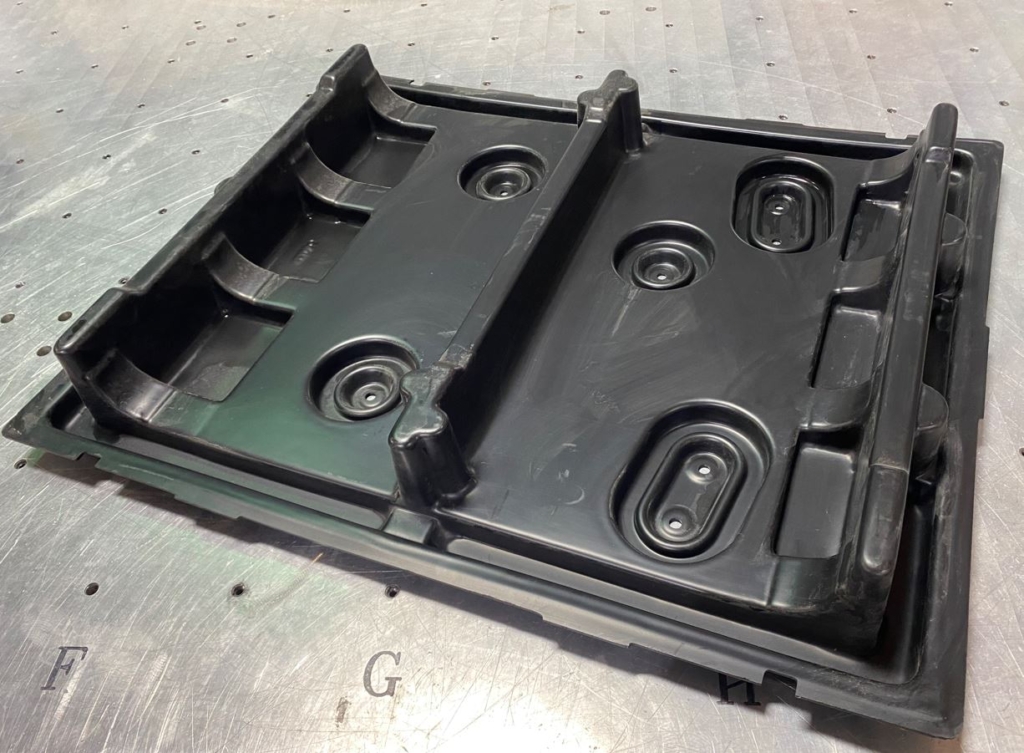
Manufacturing facilities and assembly lines use specifically engineered trays (or “dunnage” containers) to keep parts organized during manufacturing, packaging, and transport. You can produce custom-sized and custom-designed trays at low cost with vacuum forming, and the thermoplastics used are tough, resilient, capable of handling numerous handling cycles, and recyclable!
7. Inflow Preventers (Manhole Inserts)
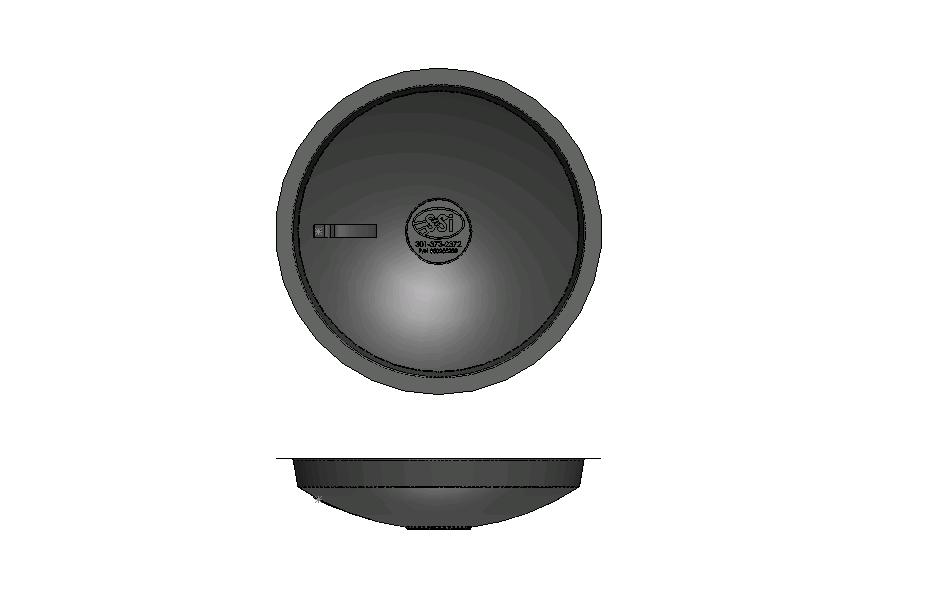
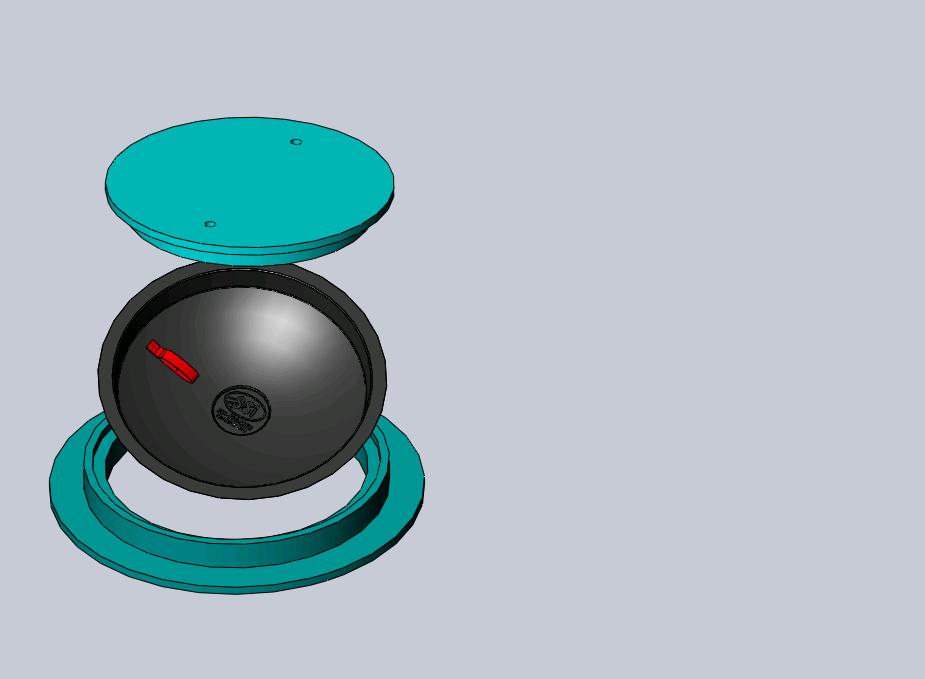
Commonly referred to as “manhole inserts,” the inflow prevention dish is a device used to limit or prevent groundwater from flowing uncontrolled into municipal sewer systems and overwhelming the treatment facility. Because many different sizes are often required to successfully prevent rainfall from entering the sewer system, manufacturers often choose thermoforming for the low tooling cost and tough, reliable material.
8. Air Ducts, Flanges, and Adaptors
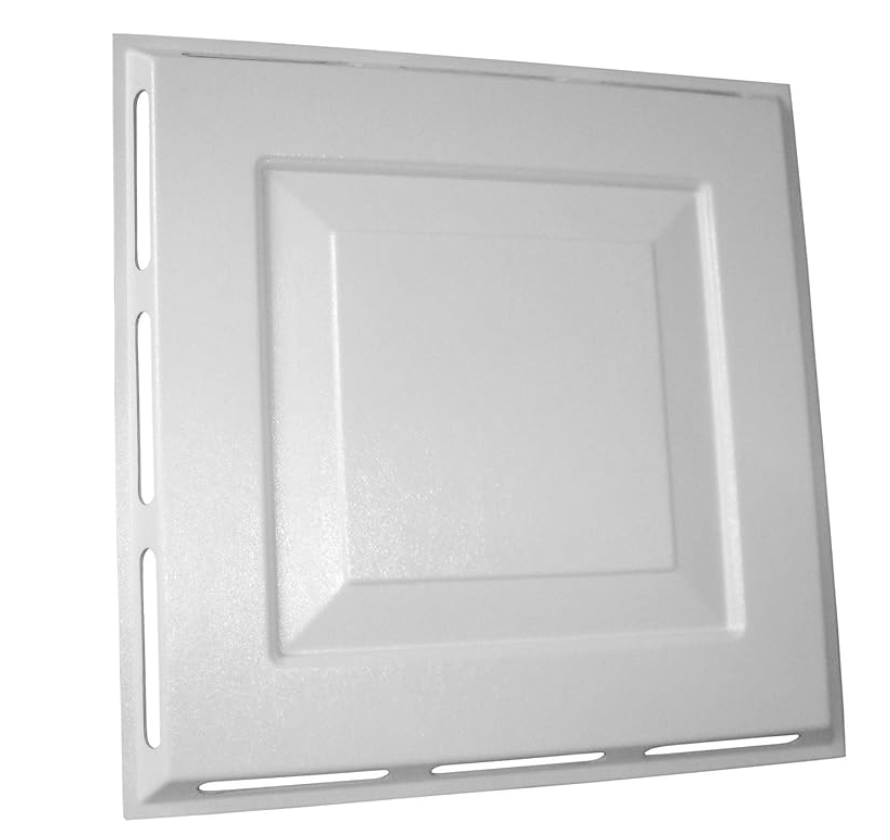
Thermoforming provides an efficient solution for adapting ventilation and airflow ductwork to fit different devices, sizes, and shapes. With thermoforming, multiple parts can be created simultaneously, which, once cut, can be assembled into intricate adapters using adhesives, hardware, or ultrasonic welding. This process enables the production of complex adapters — such as square-to-round transitions, corner adapters, or flanges — at a low cost, making it ideal for solving complicated transition challenges. Additionally, thermoformed ductwork and adapters can feature durable, weather-resistant finishes to meet both functional and aesthetic requirements.
9. Funeral Care Trays
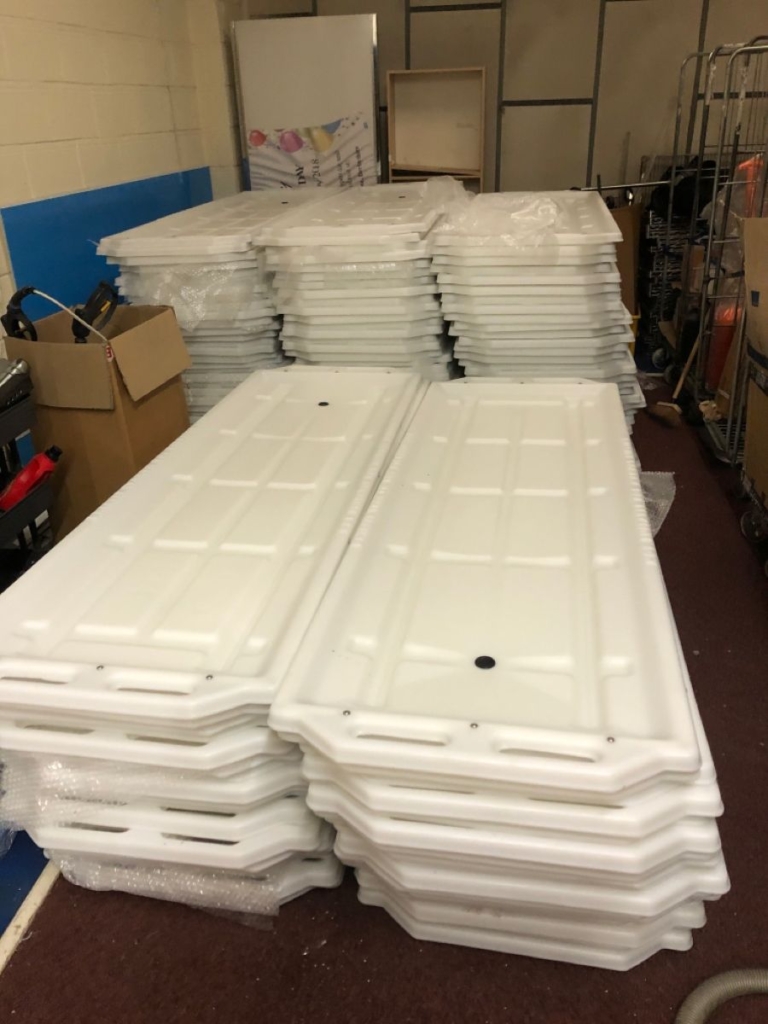
Thermoformed trays made from durable high-density polyethylene (HDPE) are commonly used for applications such as mausoleum trays, flower trays, carts, and display fixtures because they offer cost-effective reliability and can be used indoors and outdoors without much maintenance.
10. Medical Items
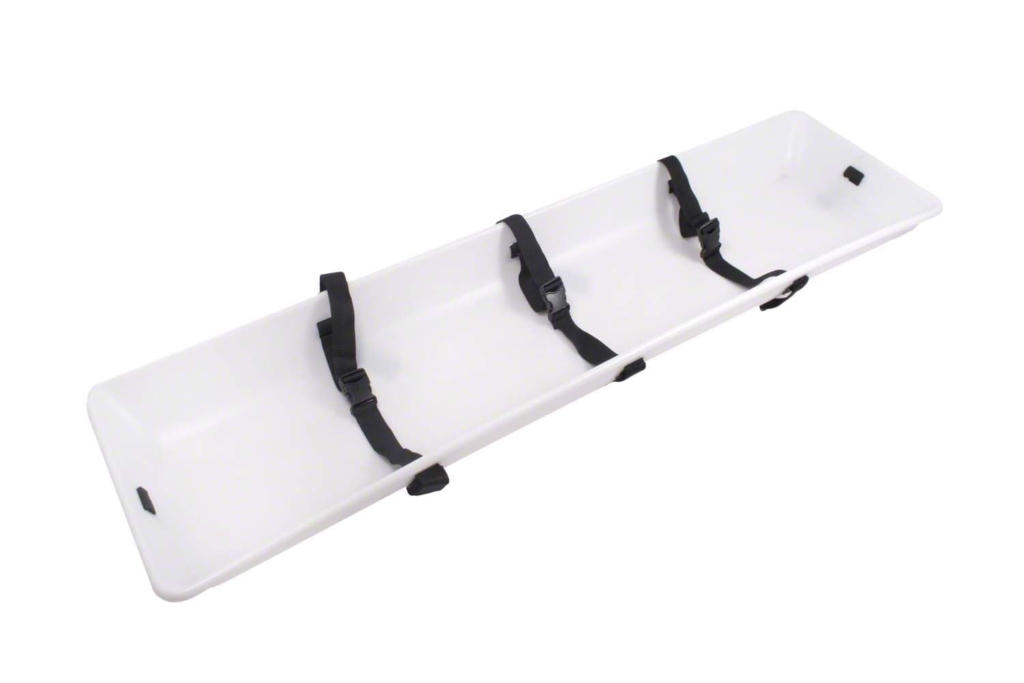
While many plastic items in the medical field are injection molded, thermoforming is also widely used for producing components like instrument housings, imaging device enclosures, hospital furniture and bed parts, testing carts, and medical waste containers.
Thermoforming offers two key benefits for medical items:
- Thermoplastic materials tend to be easy to clean and sterilize, making them a good fit for environments with strict hygiene standards.
- It’s easy to vacuum form components with textured surfaces, which can make objects easy to grip for both practitioners and patients.
11. Mass Transit Panels
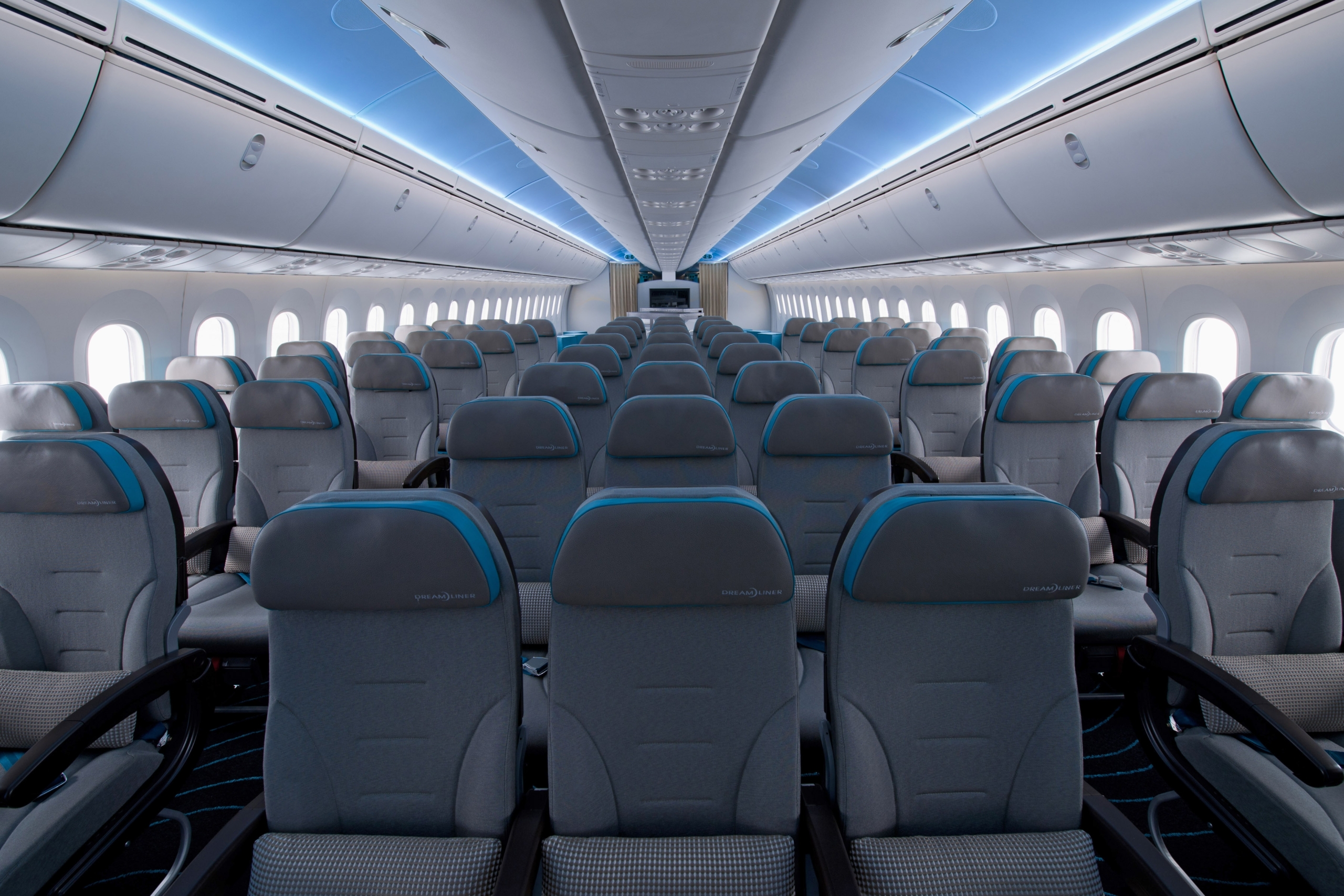
Panels — including wall panels, furniture, and window and door trims — in buses, airplanes, subway cars, and trams are often thermoformed. Materials can be selected that will minimize scratches and scuffs, resist graffiti, require little to no maintenance, and be easy to remove when needed.
12. Piling Caps (Post Caps)
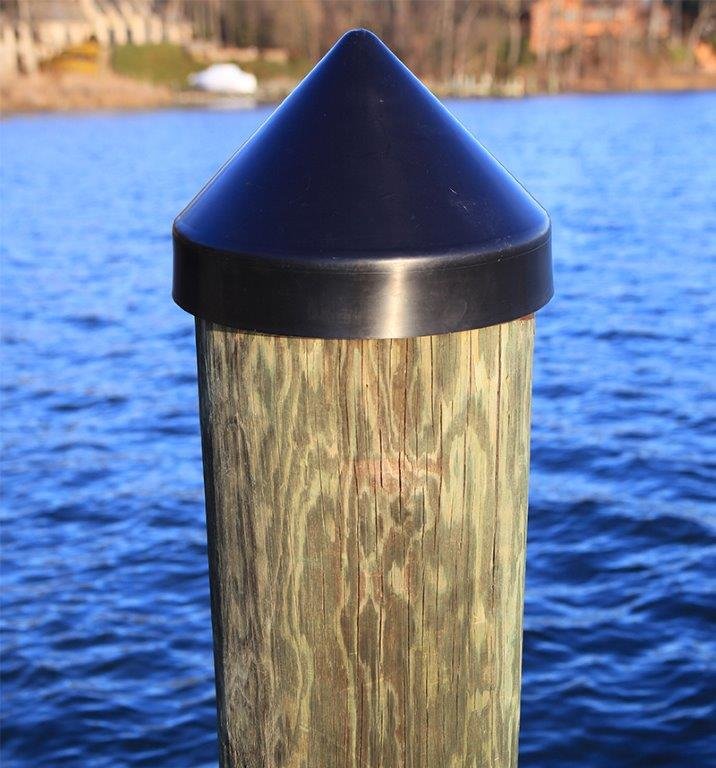
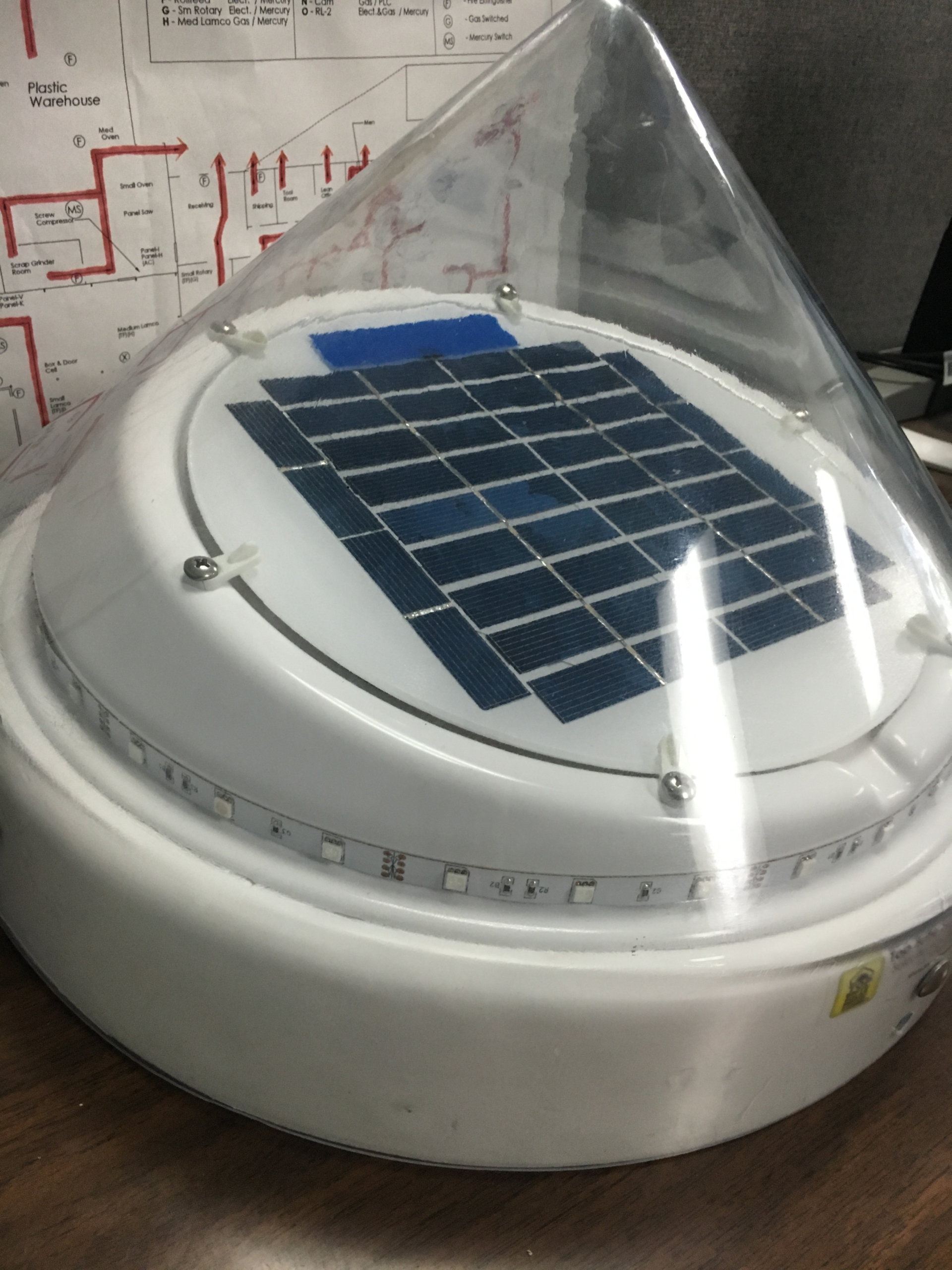
Pilings, fence posts, and even utility poles must withstand long exposure to weather and animals, like birds, that use them as perches. Both of these can cause significant damage over time, but thermoformed variants of these products are incredibly durable, with a lifespan often over a decade, even in direct sunlight and weather. These plastic caps are also easy to install, flexible to fit over irregularly shaped posts, can be customized in different shapes, and offer good protection for a price hundreds to thousands of times cheaper than the cost of piling or pole replacements.
13. Kitchen Appliance Components
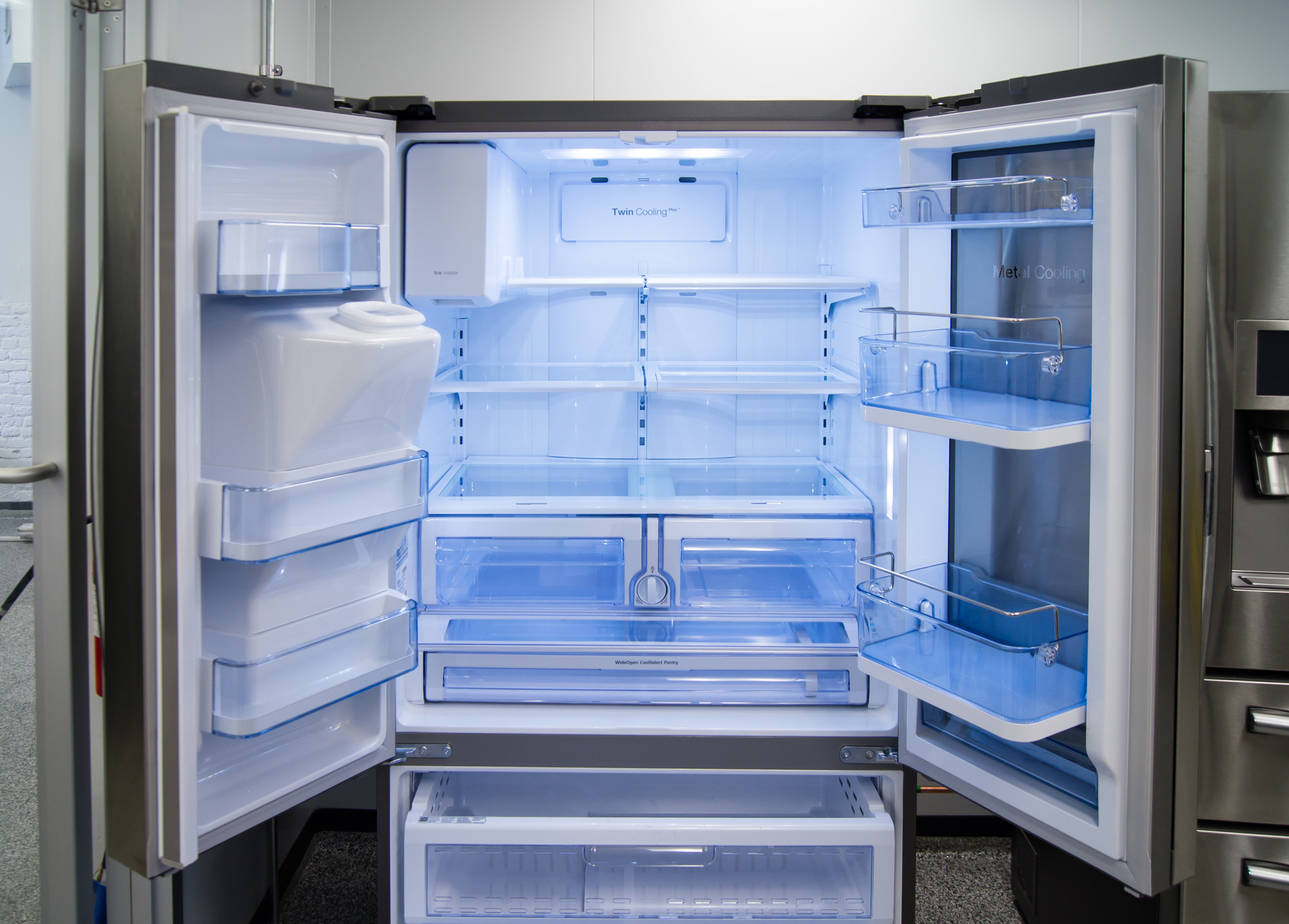
The fact that refrigerators often contain a thermoformed liner is generally well-known, but there are many more items in the kitchen that can be thermoformed, too:
- Silverware organizers
- Vegetable and fruit bins
- Mixer and cutter housings and covers
- Serving trays
Many popular mixing, slicing, and other cooking and food preparation items are thermoformed (or have thermoformed housings or covers) to save weight and make them easy to clean.
14. Furniture
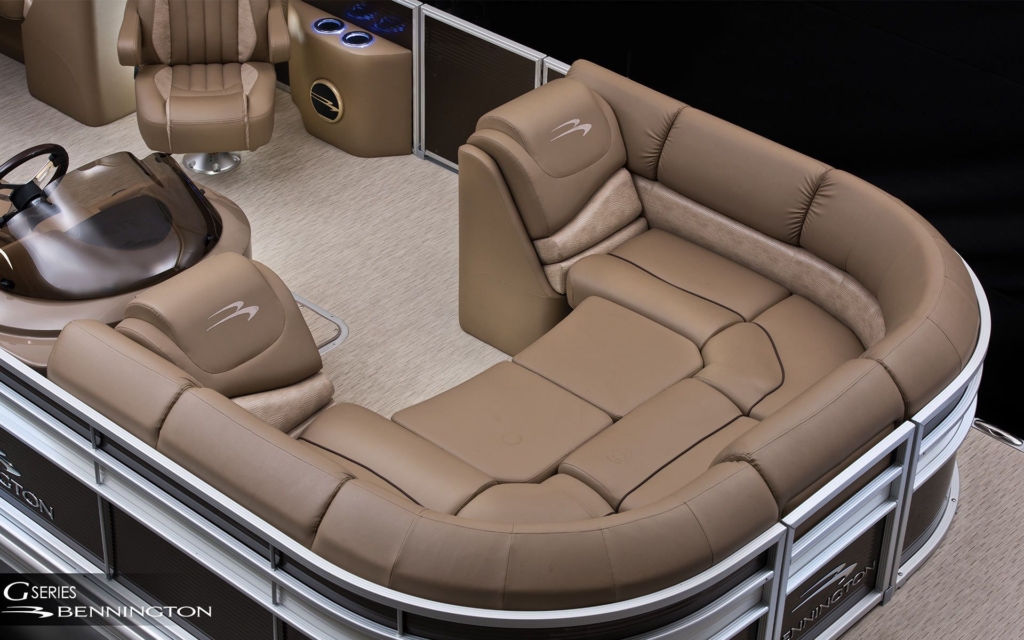
Many common pieces of furniture can be thermoformed, most notably the scalloped plastic chairs used in schools and at events, as well as:
- Stadium seats
- Seat backs for upholstered seating
- Tables
- Armrests
- Dressers
- Makeup stations
The benefits of thermoforming furniture include:
- Produce highly featured large furniture parts with reasonable cost and high reliability
- Withstand rust and rot (unlike metal and wood)
- Easy to color and upholster
- Weather-resistant, UV-resistant
- Lighter than wood, metal, and fiberglass
15. RC Toys, UAVs, and Drones
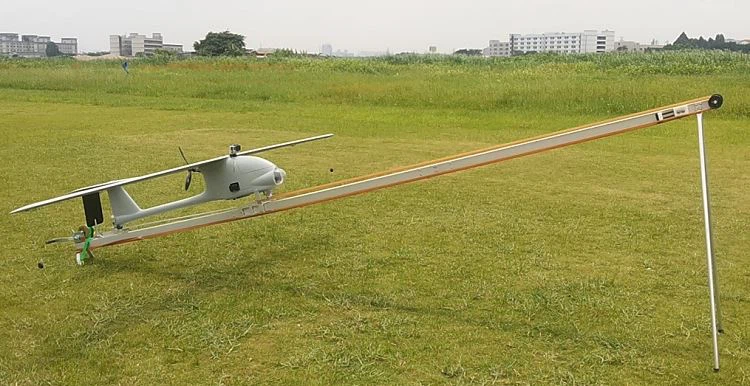
Thermoforming can create light, strong, impact-resistant bodies for radio-controlled toys, vehicles, and drones that see frequent recreational use. Drones may even need to weather some extreme environmental conditions (think of a weather station drone monitoring storm damage) — and thermoplastics can handle it!
Get Custom and Stock Thermoforming Products
Thermoforming has some consistent advantages when it comes to producing products. If you look through the product examples we’ve listed, you’ll see some common themes, like:
- Cost-effective
- Great for large parts
- Flexible design options
- Easy to customize
- Low maintenance
- Sustainable and recyclable
- Durable and weather-resistant
- Lightweight, yet strong
While thermoforming certainly can’t be your only manufacturing process, you could likely use it more than you are right now. Are there any products featured here that you produce using another method? If you’re interested in switching to thermoforming, reach out to us — we’re standing by to help you find the right method and material for your project.
Want more examples of products we frequently vacuum form here at SSI?
Check out our catalog — but remember, you aren’t limited to what you see here!
View Our Catalog Products