Fiberglass Vs. Plastic & When to Choose Thermoforming
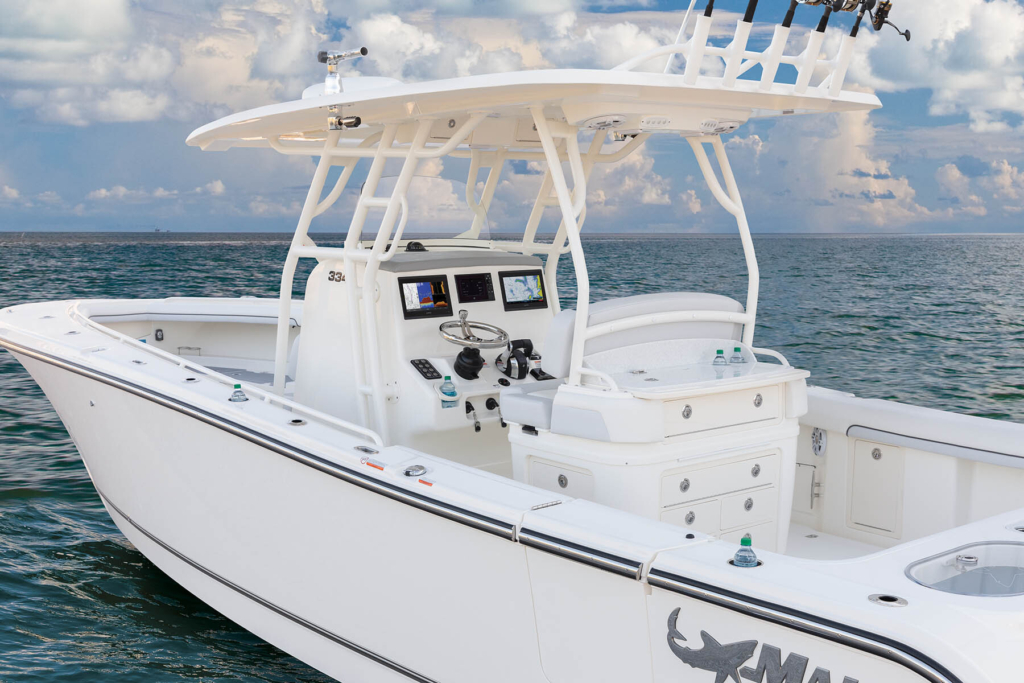
Are you currently using fiberglass in your manufacturing processes? You might be able to make the switch to plastics. In this article, we’ll cover what you need to know about fiberglass, plus:
What to Know About Fiberglass?
Fiberglass combines resin and glass fibers to produce two key benefits of plastic and glass: formability and strength. When we compare it to plastic in this article, it’s important to note that we are talking about thermoplastics. Fiberglass is itself technically a reinforced plastic, and, more specifically, a composite thermoset. This means fiberglass, unlike thermoplastic composites, cannot be reformed once it has set. This limits the forming methods available for fiberglass and contributes to its higher price point. Additionally, the fiberglass forming process involves chemical exposure and thus requires a high level of expertise and experience in fiberglass tool making and production.
Advantages of Fiberglass
There’s a good reason fiberglass has been a mainstay material in manufacturing for so many years. When compared to other common manufacturing materials like metal, wood, and concrete, fiberglass has many advantages:
- Good resistance to corrosion and degrading
- More moldable and customizable
- Requires less finishing work
- Good sound absorption
- Cost-effective
When to Use Fiberglass vs. Plastic
It’s clear that fiberglass has many beneficial properties, but is there a compelling reason to choose fiberglass over thermoplastics in an application where either might be used?
Let’s take a look at the various factors you’ll need to consider and see which material “wins” when it comes to each.
Cost: Plastics Win
One of the most significant advantages that thermoplastics offer over fiberglass is price point, thanks to these thermoforming characteristics:
- Largely automated — less labor needed
- Faster production rate
- Less tooling required for completion
“If a manufacturer produces a part out of fiberglass instead of thermoplastics, they are significantly more invested in that one part,” says Kyle Wirt. “The time and materials lost are higher, and determining the end result of a completed part takes up to 3 hours. Thermoformed parts can be determined in a few minutes.”
Order Volume: Plastics Win
While neither vacuum forming nor fiberglass molding is the best choice for enormous order volumes, vacuum forming has the edge due to its lower cost and faster production rate.
Time: Plastics Win
Thermoforming comes with a higher production rate, meaning lead times for plastic components are typically shorter than for fiberglass parts.
“Many fiberglass manufacturers that produce small-to-medium size parts in small-to-medium size quantities typically build each part by hand, versus a thermoforming machine that produces parts every few minutes, says Kyle Wirt. “The main advantage for plastics is that we can produce many parts off of a single mold.”
Strength: It Depends
Fiberglass has historically been stronger than thermoplastics, though advances in thermoplastic technology in recent years have closed this gap substantially. Choosing the best fit based on strength is by no means the cut-and-dry decision it once was, though fiberglass may still have a reputation for strength.
But, as SSI plastic expert Kyle Wirt says, “It really depends on how you are measuring strength and what factors you need to consider. At this point, strength isn’t really a relevant argument when deciding.”
Large Size Parts: It Depends
Fiberglass can be a better option when you need to create a component of significant size, but this depends on your vacuum forming options. Since thermoforming uses plastic sheets, you can come up on limitations in the size of sheets available, which then limits the size of the components you can thermoform.
“But there are many ways thermoplastic can be manufactured to make thick and tall parts,” says Wirt. “Plastic is the better choice for quality, redundancy, and cost.”
Weight: Plastics Win
Plastics are the clear winner here. Thermoplastic components are generally lighter than their fiberglass counterparts — highly desirable if you’re trying to reduce weight.
Eco-friendliness: Plastics Win
Fiberglass materials can’t be recycled. This, along with the chemicals and toxic materials used to form fiberglass, means fiberglass is not the most eco-friendly option. With thermoplastics, we can recycle scraps and even whole components, plus we avoid the chemical processes needed for thermosetting.
What Plastic Types Compare to Fiberglass?
When looking at thermoplastics that would typically be used in place of fiberglass, we generally see TPO and ABS. TPO is typically used on cosmetic parts, while ABS is a more common replacement for fiberglass.
“Many of the cosmetic parts that we make at SSI are acrylic capped ABS to add shine and UV resistance,” says Wirt. “Anything that isn’t cosmetic or that will get wrapped in vinyl, leather, rubber, etc., would be ABS. But we can swap the wrapped process for TPO, too, if that’s the customer’s preference.”
Fiberglass vs. Plastic in Marine Manufacturing
Marine manufacturing is one of the few fields that still frequently uses fiberglass. The issue with fiberglass marine components, however, is that they are time-consuming and costly to replace. Since plastic offers comparable benefits in terms of UV, water, and resistance, a lot of SSI’s expertise comes from replacing fiberglass marine parts with more economical plastic versions.
“All of our boat-building customers come to us to replace their fiberglass, sheet metal, and wood parts,” says Wirt. “Everything in our catalog for marine retrofitted parts used to be made out of fiberglass and wood.”
Reverse engineering parts made of fiberglass has been a significant part of SSI’s history:
“Boat builders can cut out a piece of their boat and send it to us,” says Wirt. “We can reverse engineer it and develop a plastic replacement part for mass production.”
Switch to Plastic with SSI
Need new components and don’t want to wait or pay for costly fiberglass replacements? We can help you make the switch to plastic. Just let us know what you’re working on and we’ll get back to you with our recommendations!
REQUEST A QUOTE