3D Printing & Thermoforming: Competitors or Colleagues?
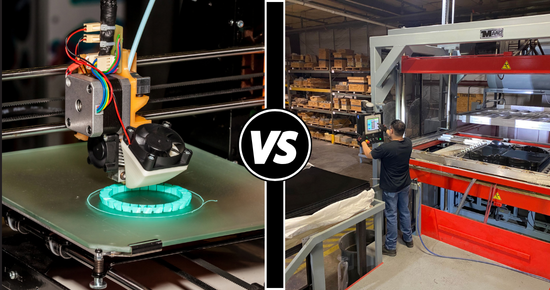
Are you currently using fiberglass in your manufacturing processes? You might be Trying to figure out whether 3D printing or thermoforming is right for you? While there are some situations where 3D printing is an alternative to vacuum forming, they each have their own strengths and use cases and can even join forces to speed up manufacturing! Read on to learn more about how these two methods differ from and complement each other:
How does 3D printing compare to vacuum forming?
While thermoforming (vacuum forming) involves heating and molding plastic sheets, additive manufacturing builds components in layers by pushing plastic material through a nozzle. This extrusion is similar to the general method used in injection molding, although the processes differ significantly and lend themselves to unique use cases.
Method
Both 3D printing and vacuum forming use CAD software to create 3D models. For vacuum forming, these models serve as the basis of the mold design. For additive manufacturing, designers must take an additional step with slicing software to prepare the model for printing in layers.
Materials
While both methods use plastics (ABS and PETG being the common denominators), 3D printing has many more options, including metals, resins, and ceramics.
Post-production requirements
Following main production, components created with both methods typically need some amount of finish work. For vacuum forming, we need to trim excess material from the part. 3D printing parts may require more work to remove supports and polish.
Prototyping
While 3D printing is the big name in rapid prototyping, you can also vacuum form prototypes (and we offer this at SSI!). The vacuum forming process we use allows us to create prototypes faster than in some other methods of plastic forming. As we’ll see in the next section, however, there are many factors to consider when choosing 3D printing or vacuum forming.
Should I choose 3D printing or vacuum forming?
Choosing one method over the other isn’t too tricky when it comes to additive manufacturing and vacuum forming. Every situation is unique, but there are some typical scenarios in which the choice can be fairly clear-cut.
Choose 3D printing when you…
- Need an intricate and detailed geometry that thermoforming can’t achieve
- Have a very low production volume
- Can’t invest in thermoforming tooling costs
- Will likely iterate on your prototype design several times
- Want to produce customizable pieces (most relevant to consumer goods)
- Can’t use plastic as a material
Expert Insight:
“3D printing’s best attribute is also its best use/application. It allows the production of a physical part for evaluation without incurring the cost of tooling.” – John Donato, SSI President
Choose vacuum forming when you…
- Need to produce large, thin parts
- Require food-safe items
- Want to use transparent materials
- Expect a higher production volume
- Have a run of items for which uniformity is key
- Need to create highly durable components
Expert Insight:
“Thermoforming can produce parts much faster than 3-d printing and with surfaces and features that 3-d printing cannot. The best case for choosing thermoforming is when the quantity required makes printing them one at a time no longer feasible, or when the part needs surface features that 3-d printing cannot produce.” – John Donato, SSI President
Using 3D printing alongside thermoforming
We’ve talked about the distinctions between these two manufacturing methods, but the real beauty of the rise of 3D printing is that it lends itself so well to supporting thermoforming. Designers and engineers can now develop actual 3D components in early stages of design. This allows manufacturers to measure, fit, and test new components before creating a thermoforming mold, making it easier to iterate on new designs to achieve the best end result.
Some thermoformers may use 3D printing in the tooling process to create CNC and assembly fixtures. In some cases, you may even be able to 3D print the mold for vacuum forming!
Once 3D printing has sped up the design and tooling processes, thermoforming can then take over and quickly produce finished components.
SSI Use Case: 3D-printed prototypes
We worked with an aerospace company that designed and 3D printed a prototype part for UAVs (unmanned aerial vehicles). When the design passed from prototype to production, they found that each part took several hours to complete using a 3D printer.
While 3D printing was a great way to finalize the design, it wasn’t ultimately feasible to continue at scale. SSI stepped in and, using the 3D printed prototype provided, built a thermoforming tool and process to quickly form multiple parts at a time.
By using both methods in harmony, we fast-tracked the design process and took a production rate of one part per several hours to six parts per several minutes!
Step up your production efficiency with SSI
Already dabbling in 3D printing? If you need to produce at higher volumes and scale your operations, SSI’s vacuum forming services can help! We can start working from your 3D-printed prototype or mold.
Check out our process to see how it works!