Thermoforming Polycarbonate vs. PETG vs. Acrylic: Finding the Best Clear Plastic for Vacuum Forming
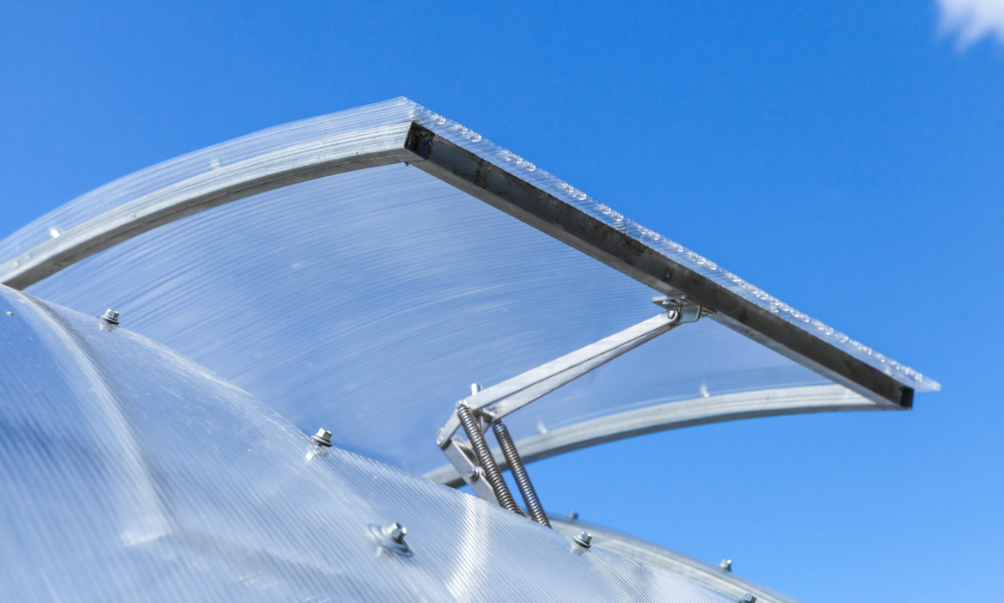
Need a clear plastic part to finish your manufacturing project? We sat down with John Donato, SSI President, to discuss what you need to know when picking your materials:
“When considering molded or fabricated parts made from clear plastic materials, you’ll often find that the material options are lumped together or used interchangeably. This can be a real problem since your main options are very different materials. Luckily, the attributes for each are well known, making the proper material for your parts a “clear” choice!”
In this article, we’ll explore polycarbonate, a common clear thermoplastic, compare it to acrylic and PETG, and take a look at some of our past projects involving these materials.
What is Polycarbonate?
Polycarbonate, abbreviated PC and also known by the trade name Lexan®, is a thermoplastic material well-known for its impact resistance and toughness as well as its clarity and light transmission. In some applications, polycarbonate is strong enough to be considered as an alternative to metal, and, while its clear surface can be scratched, it is nearly impervious to breakage — meaning it is also a great substitute for glass. Additionally, as an engineering resin, PC has enhanced performance characteristics over cheaper commodity resins.
We often see polycarbonate in applications where strength and clarity are essential:
- Skylights
- Electrical parts
- Safety helmets
- Lenses for lights (e.g., automotive headlight covers)
- Lenses for glasses
- Medical devices
- Viewing windows and clear covers
How Polycarbonate Responds to Vacuum Forming
“Producing parts from polycarbonate is relatively straightforward,” says John. “But it can be temperamental to heat form.”
This “temper” is often why polycarbonate components tend to be relatively expensive:
- PC must be dried before it can be thermoformed, adding extra time to the process.
- The material can be susceptible to heat shrinkage and defects like bubbles and stress whitening; avoiding these requires careful design considerations and precise temperature control throughout production.
- PC may be better suited to simpler shapes, as complex geometries increase the difficulty of forming and tooling.
Despite its “temper,” if you choose an experienced manufacturing partner, forming polycarbonate parts can indeed be “relatively straightforward.” In the right hands, PC is quite versatile and can be thermoformed, cut, drilled, threaded, glued, printed on, and even ultrasonically welded.
Is Polycarbonate the Right Clear Plastic for You?
If you need transparency, durability, and impact resistance for a demanding application, polycarbonate is a great choice.
But there are some disadvantages to consider, in addition to its cost and the forming challenges we mentioned above:
- You might not always want a material as rigid as polycarbonate — many applications demand a more flexible material.
- Polycarbonate’s strength is not without imperfections; it is susceptible to both scratches and cracks. This stress cracking, or “crazing,” is especially common in wet (or even moist) environments. This often comes up with polycarbonate headlight covers, though these are still a popular choice in the automotive industry.
- While PC is UV stable, it can yellow if exposed to sunlight over time.
Polycarbonates contain BPA, which has come under scrutiny in the past few years as a potentially hazardous chemical. The concern is generally about its use in food and beverage products, but some people may still be concerned about potential contact via air, dust, and water (see NIH.gov for more info).
SSI Polycarbonate Case Study: Camper Skylights
“We frequently work with manufacturers in the recreational vehicle industry, and we discovered that polycarbonate is a great option for a camper’s domed skylights. The client we worked with was using an opaque material for this, which severely limited the amount of light coming into the vehicle. With polycarbonate’s great clarity, we were able to let warm, natural light into the interior. Campers need to reliably protect you from the elements, but polycarbonate makes that possible without compromising on interior aesthetics.”
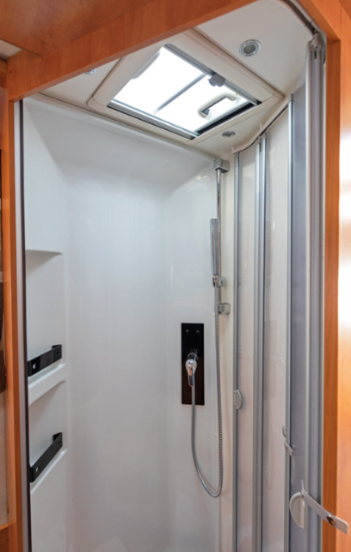
Polycarbonate vs. Acrylic
Acrylic (also known as polymethyl methacrylate, PMMA, and plexiglass) is a common resin and another clear plastic you might choose for your thermoformed components.
Some common applications include:
- Windows
- Sneeze guards and retail dividers
- Point of purchase displays
- Lighting and architectural
- Aquariums and terrariums
- Solar panels
- Signage
- Instrument and gauge lenses
Plexiglass, Plexiglas®, and Cell Cast Material
Before we dive in further, we should clarify something about the material’s name. Plexiglass is a common, non-branded term for acrylic, while Plexiglas® (spelled with one s), is a trade name for a specific type of acrylic sheet developed by Röhm & Haas.
This distinction is important because materials described as plexiglass may be either extruded or cell cast acrylic, while Plexiglas® is always cell cast material. The cell cast process imparts different properties than the extruded sheet process, and recognizing this difference can help ensure you choose the right material. Cell cast sheets have better light transmission, fewer defects, better chemical resistance, and are stiffer and stronger than their extruded counterparts, though they are also more expensive.
When to Choose Acrylic Over Polycarbonate
Though not as strong as polycarbonate, acrylic offers some other highly prized qualities:
- Clearer, better at insulating, and two times lighter than glass
- Does not lose clarity during the forming process
- Very affordable
- Excellent weatherability; often used as a glossy protective layer over other plastics
- Resistant to a variety of common chemicals
- Easy yields reproducible parts
- Can be fabricated by cutting, drilling, etc.
Choose acrylic when you need plastic that is clear, cheap, weatherable, and strong, but be aware of the potential drawbacks, too:
- Fairly easy to scratch
- Can distort under high temperatures
- Requires special care to prevent cracking or shattering during fabrication
- Cracks may create dangerous sharp edges
- Can be severely and permanently damaged by a variety of chemicals, including alcohols, ketones, halogens, and even glass cleaner
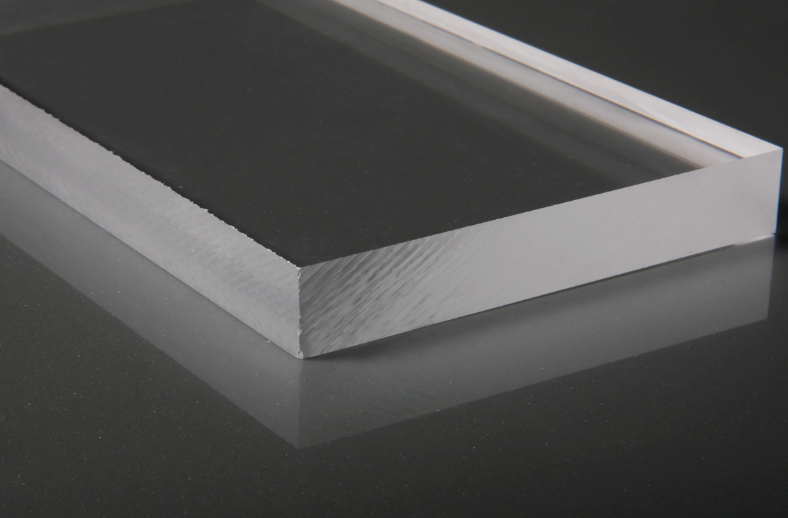
SSI Acrylic Case Study: Mixer Covers
“One of our projects involved commercial mixing machines. The original cover for these was opaque — something of a disadvantage if you need to see what you’re making. We created custom acrylic covers based on the original design that fit the machine perfectly while allowing operators to see the contents while mixing.”
PETG vs. Polycarbonate and Acrylic
PETG (sometimes referred to by the trade name Vivak®) is an enhanced version of polyethylene terephthalate or PET, a common material that’s particularly associated with plastic water bottles. The addition of glycol (G) to PET yields PETG, a stronger, more durable material. Some typical uses of PETG include:
- Thermoformed trays
- Medical equipment and prosthetics
- Machine guards and safety devices
- Personal protective equipment
- Toys and games
- Sporting equipment
- Tanks and sight glasses
- Viewing windows and clear covers
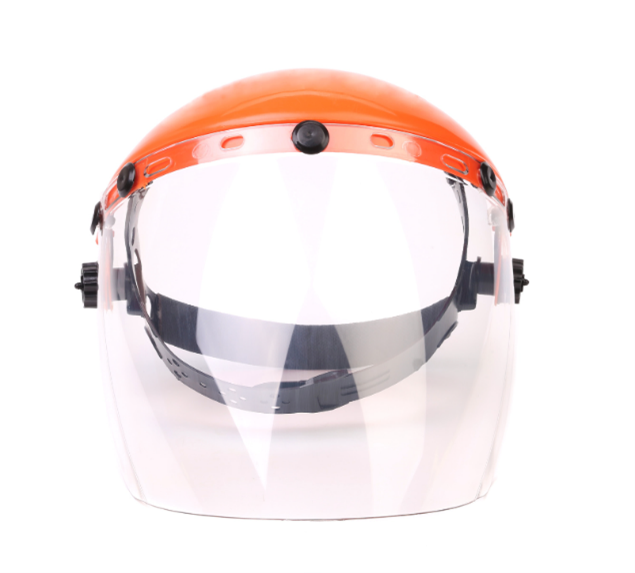
When to Choose PETG Over Polycarbonate or Acrylic
“PETG is sometimes referred to as the ‘poor man’s polycarbonate’ because it’s almost as strong but far less expensive,” says John.
It’s true! For its price, PETG offers some great benefits when compared to polycarbonate and acrylic:
- Does not leave sharp edges like acrylic
- Virtually unbreakable (close to —but not quite — as strong as polycarbonate)
- High impact resistance than acrylic
- Easy to mold
- Lends itself well to deep draws and intricate details
- Doesn’t require drying time; shorter processing time overall
- Can be bonded with adhesives, machined, ultrasonically welded, and decorated by painting, silk screening, or hot stamping.
- Economical and easily recycled
With all that said, PETG is not always the answer:
- Not as clear as acrylic or polycarbonate
- Can scratch, but less likely than acrylic
- Lower impact resistance than PC
- Relatively low UV resistance; better suited for indoor applications
SSI PETG Case Study: Terrariums
“PETG was a clear choice when it came to a project we worked on involving terrarium-style grow pot enclosures. Since these need significant depth to allow plants to reach their full growth potential, and PETG is so well suited to deep draws — and allows light in along with a viewing window — it was the perfect fit for this application.”
Get Experienced Support with Clear Plastic Components
Knowing the different attributes of these common clear plastics will help you choose the best material for your application, but you certainly don’t have to go it alone.
At SSI Custom Plastics, we have extensive experience in molding and fabricating polycarbonate, acrylic, and PETG, and we can help you find clarity when it comes to selecting the right plastic. Just tell us what you need!